Reaktywacja wielkiego pieca po innowacyjnej modernizacji w dąbrowskim oddziale ArcelorMittal Poland
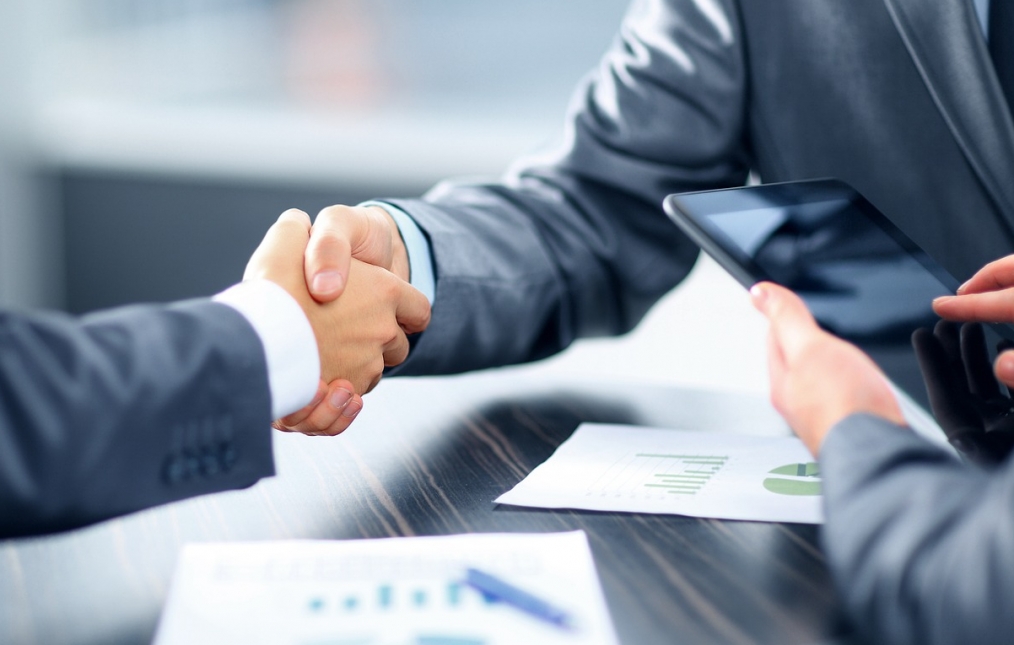
Odzyskał swoją dawną aktywność wielki piec o numerze 2, znajdujący się w oddziale firmy ArcelorMittal Poland w Dąbrowie Górniczej, po zakończeniu jego kompleksowej modernizacji. Inwestycja ta, której wartość przekroczyła 720 mln zł, miała na celu nie tylko zwiększenie efektywności produkcyjnej, ale także ograniczenie emisji takich zanieczyszczeń jak pyły i dwutlenek węgla.
Prace nad modernizacją rozpoczęto pod koniec marca. Wśród licznych działań podjętych w ramach tej inwestycji znalazły się między innymi wymiana wyłożenia węglowego wewnątrz pieca, stworzenie nowego systemu chłodzenia oraz budowa zaawansowanej technologicznie oczyszczalni gazu wielkopiecowego. Rezultatem tych rozległych działań jest znaczne ograniczenie negatywnego wpływu huty na środowisko naturalne, a konkretnie redukcja emisji CO2 o niemal 45 tys. ton rocznie.
Podczas realizacji modernizacji, ArcelorMittal Poland wprowadził do swojej infrastruktury dwa projekty badawczo-rozwojowe. Pierwszym z nich jest innowacyjny układ chłodzenia o zamkniętym obiegu, a drugim to wysoka na ponad 100 metrów proekologiczna oczyszczalnia gazu wielkopiecowego.
„Inwestycja ta była naprawdę ogromna” – mówi Michał Kocot, kierownik remontu wielkiego pieca nr 2. „Poza typowymi pracami jak wymiana bloków węglowych czy płyt chłodzących pancerz pieca, gruntownie odnowiliśmy system odpylania hali lejniczej. Zainstalowaliśmy również nowy układ załadunku pieca i zestawy dyszowe o zmienionej konstrukcji, a także nowoczesny system automatyki i kontroli procesów.”
Dzięki implementacji nowego układu chłodzenia oraz instalacji wymienników ciepła, spółka zdołała poprawić efektywność procesów oraz zmniejszyć dodawanie wody do obiegu chłodzenia zestawów dyszowych nawet o 85%. Inwestycja ta umożliwiła także obniżenie zużycia energii elektrycznej o prawie 400 MWh rocznie oraz redukcję emisji CO2 o blisko 45 000 ton rocznie. Również emisja pyłów została ograniczona – teraz ponownie wykorzystywanych jest ponad 18 000 ton pyłu. Ponadto udało się zmniejszyć ilość produktów ubocznych powstających w procesie – nawet o 70%, jak również zredukować poziom hałasu w obrębie instalacji.